Crate & Barrel
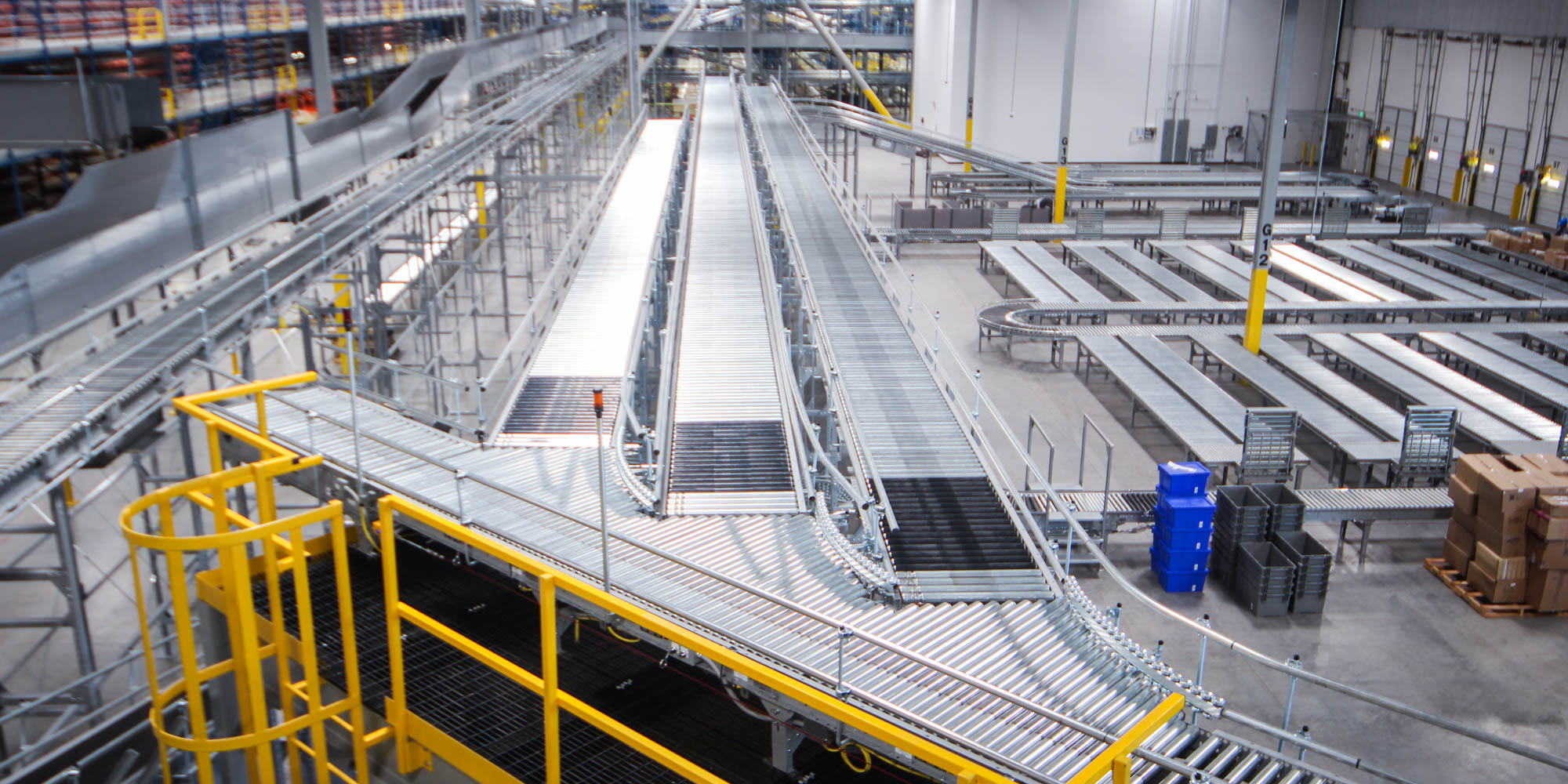
Quick Facts
Crate & Barrel is a leading retailer in housewares and home accessories.
Crate & Barrel, a leading retailer specializing in housewares and home accessories, sought ways to manage their operation and material handling costs while operating separate direct fulfillment and retail store replenishment facilities. Ensuring top quality specialty products at a value price point is their offering cornerstone. Whether Crate & Barrel is direct shipping an exquisite handmade glass from Poland to one of their online shoppers, or routing a truckload of bedding, furniture, mugs and cutlery to 170 retail stores nationwide, they strive for the highest accountability. Securing a competitive operation to support that goal required a unique material handling process and solution that only Daifuku-Wynright could provide.
Challenge
The primary challenge was to determine, design and build a scalable system to keep pace with rapid growth and inventory complexities. With an already significant retail store business now augmented by internet, catalog and gift registry orders, Crate & Barrel required a broad-based solution to manage a broad range of complexities. Consolidating retail store and direct purchase fulfillment from a single distribution center and pooled inventory meant that Wynright’s process analysis would need to anchor their proposed solution.
Solution
Daifuku Intralogistics America worked closely with Crate & Barrel to evaluate and account for every possible distribution scenario, designing a scalable solution for their burgeoning business. Drawing on a full material handling product portfolio, Daifuku Intralogistics America included a broad range of products in the automated conveyor system, which comprised three-tier pick modules, value-add workstations, pick verifications stations, pack stations, sliding shoe and pop wheel sortation, and cross-docking capabilities. The facility ships an average of 35,000 cartons per day, peaking at 70,000 per day during the holiday season. Product damage has been reduced by 50% and returns have been reduced to less than 2%.
Outcome
By consolidating both retail store replenishment and direct fulfillment distribution into one operation under one roof, Crate & Barrel shares system components common to each process. Daifuku Intralogistics America’s solution has helped Crate and Barrel reduce costs, increase throughput and provide better service to their direct fulfillment. While there are still two very different processes taking place concurrently, they both source from the same inventory and share the same receiving, storage and shipping systems — resulting in a much more cost-effective and efficient operation.