ICA Supermarket
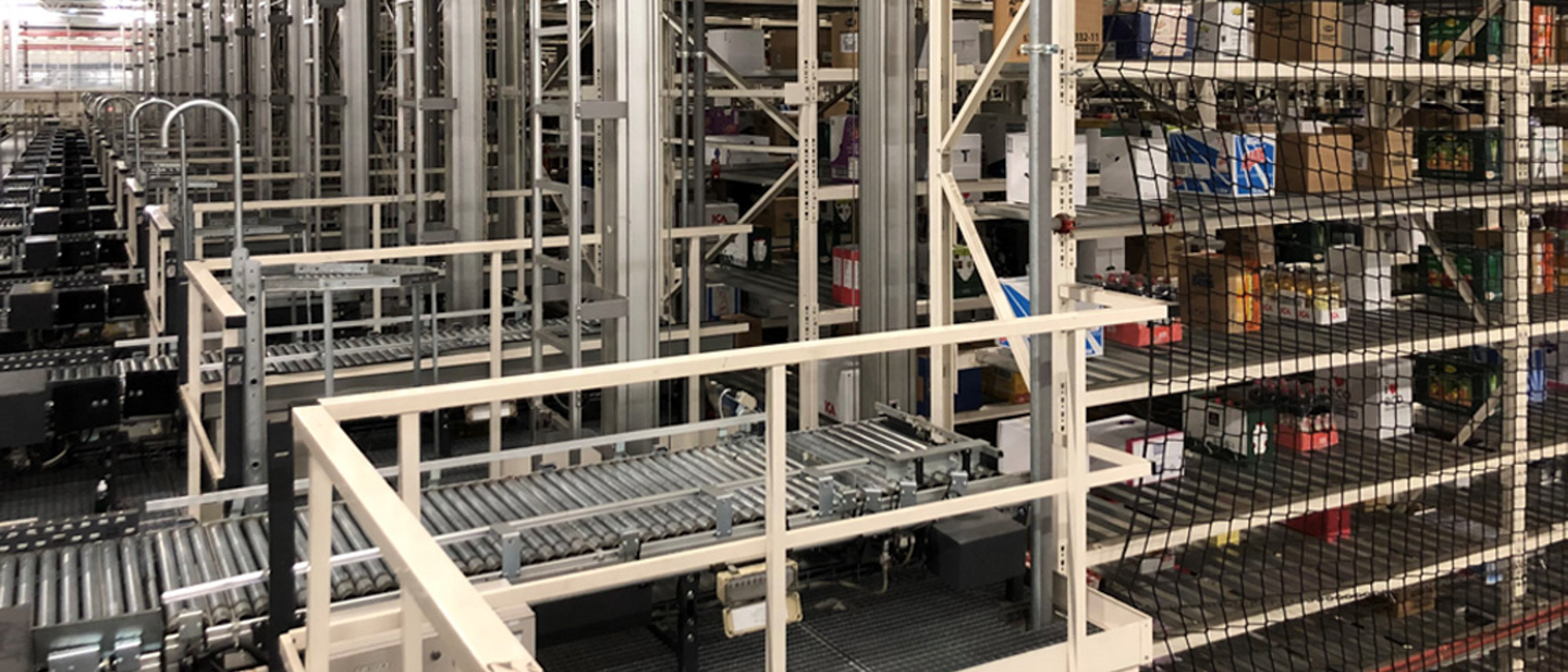
Quick Facts
ICA Sverige AB is one of the largest supermarkets in Northern Europe, operating over 2,100 stores in Sweden and other countries.
ICA consistently responds to consumer needs, providing high-quality affordable goods to consumers with its unique procurement and supply system. In 2006, the company commenced the operation of one of the largest distribution centers in Helsingborg, southern Sweden, as a supply chain hub. In May 2011, full-scale operation of material handling systems began further improving efficiency at the center.
Challenge
To consolidate 9 warehouses into one facility with 3 different temperature zones. In an effort to improve business efficiency the new facility would need to deliver dry goods (room temperature), fresh goods (refrigerated), and cold goods (frozen) in varying units and load profiles.
Solution
Dry goods are received on pallets and are carried on conveyors and Sortation Transfer Vehicles (STVs) to be stored in the unit load AS/RS (13 cranes and 26,000 locations). Goods in large quantities get separated into cases by a layer depalletizer and those in small quantities are separated by manual picking before they are temporarily stored in the miniload AS/RS (14 cranes and 14,700 locations) or on conveyor storage lines. Goods assigned to orders are retrieved from the AS/RS or storage lines and are sorted to chutes based on store location.
Fresh goods received on pallets are depalletized by a robot then are stored temporarily on conveyor storage lines. They are retrieved on a per order basis, stacked on a dedicated cart and conveyed to the shipping lines. Cold goods are managed at -16°F in the unitload AS/RS (9 cranes and 20,800 locations). The picking zone is located at the bottom of the racks, and is automatically replenished by a stacker crane that carries goods from the AS/RS. Handheld terminals are used for the picking operations to check the order location and goods.
Outcome
Material handling operations in the facility were significantly automated to obtain efficient distribution and delivery goals. Processes handling dry goods were mostly automated and shipping operations were increased while saving labor.