VSP Optics
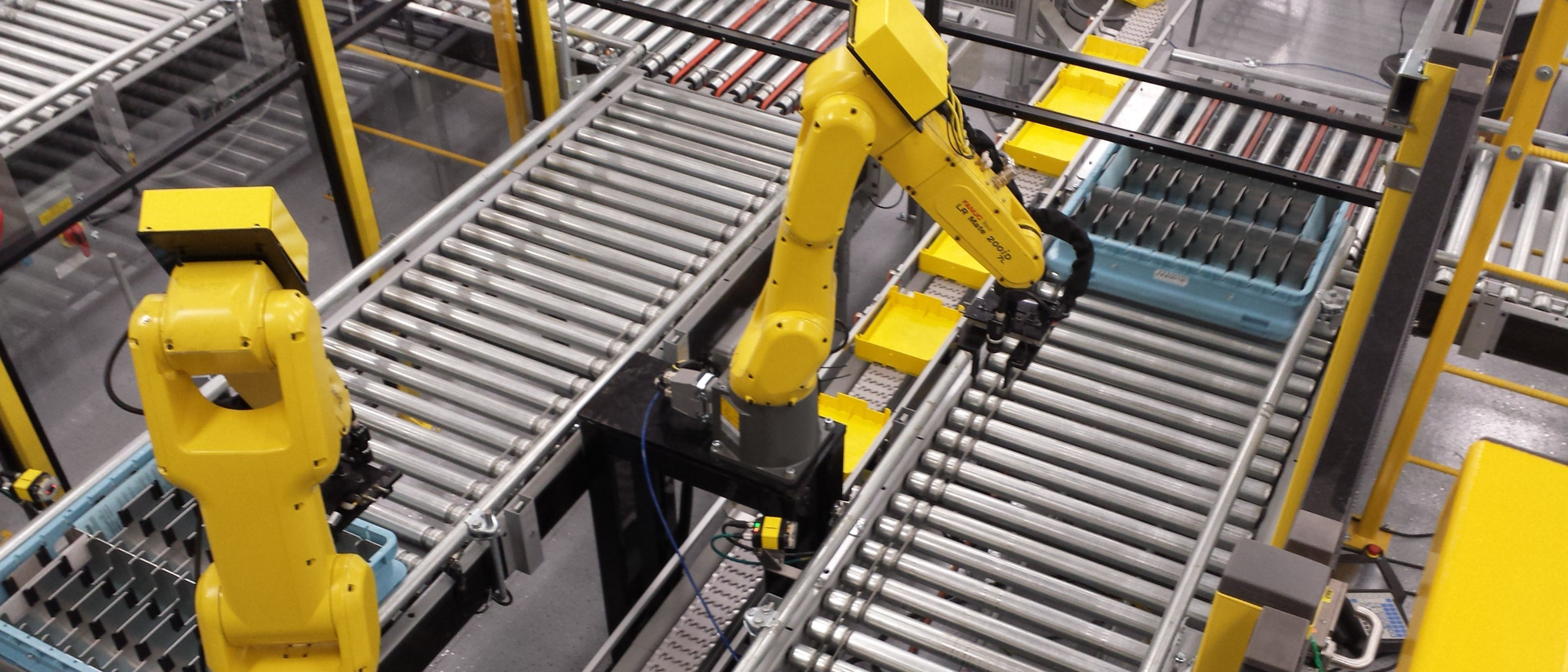
Quick Facts
VSP Optics provides ophthalmic technology, lens products and lab services that strengthen patient experience and promote practice growth.
VSP's portfolio of customized lens products is the fastest growing lens brand in the optical industry. In the midst of their tremendous growth, they reached out to Daifuku Intralogistics America’s experienced engineering and software controls team to turn their manufacturing objectives into reality.
Challenge
Online and mega optical labs are promising rapid delivery, driving a new standard in the mature and active market. This is causing optical laboratory leaders to rethink the processes by which they manufacture eyewear.
Although the lab could immediately receive a lens prescription electronically, it would typically not receive frames from an optometrist’s office for 24-48 hours. Rather than wait, they concluded that they could compress the process by starting on the lenses as soon as they got the order, giving them a 1-2 day jump on the process. However, there was still one key problem: storing the surfaced lenses until they could be matched with the right frame when it arrives.
Previous manual efforts became increasingly complicated and labor-intensive as volume increased, requiring up to 30 people in the new environment. A more cost-efficient, automated solution was needed.
Solution
Daifuku Intralogistics America logistics engineers designed a postponing, work-in-process strategy, in which items are stored and retrieved automatically until they are needed for various stages of the production process. The strategy involves placing lens materials or frames in plastic totes, where they are conveyed between an automated storage facility then onto various human and robotic assembly stations.
A Miniload storage and retrieval system, providing high density buffer storage that maximizes use of available cube space. The system can handle 26,000 frames and lenses at a time. The laboratory uses state of the art digital surfacing equipment that produces extremely precise prescription lenses which recieve various enhancements including anti-reflective coatings, sunglass and fashion tints. Next, the lenses are sent to the Daifuku H-MS to be matched up with the frame, dispatched from the eye doctor’s practice.
When the frames arrive, associates measure them for size and shape and place them into a barcode-labeled envelope and induct them into the automated system where they are matched to the corresponding lenses stored in the system or stored until the lenses are completed. The system does not care if it is storing or retrieving lenses or frames, it just looks to see if the match is already in the system. The lenses are usually done before the frames arrive, but if the frame arrives first, it is stored until the lenses are ready. Operators scan the lens or frame envelopes and the system tells them to either place it in a tote to go to the robots for matching or in a different tote for storage to wait for the corresponding match.
The robot at the first station removes an envelope from the tote and places it in a separate container at a lower level. The tote on that lower level advances to the other robot station, where the robot removes the envelope with the matching item and deposits it in the lower tote that holds the lens. This tote, which now holds both the lens and frame, advances to a station at which the matching pair is manually picked and staged prior to going into a finishing operation. Then, the lenses are cut down to size and mounted in the frame and lastly end up at final inspection process where the prescription is verified and they are ready for shipment back to the optometrist.
The process is complex and requires precision timing. Although humans are involved at the front and back end of the process, everything else is fully software driven by the warehouse execution system (WES). The software keeps a location track of all 26,000 pieces, and synchronizes the delivery of the right lenses and frames to the robotic piece-picking station. The WES is constantly re-aggregating the totes, tracking min/max levels for each tote, depleting it and filling it back up.
Outcome
The installed automation enabled the team to start work on a pair of glasses as much as 24 hours earlier than in the past, reducing the delivery time of a finished pair of glasses from 3 or 3.5 days to 2 or 2.5 days.
The system automatically stores and consolidates 6,000 orders per day (1 frame and 1 lens). To accommodate future expansion, anticipated growth rates were analyzed and the system was laid out with sufficient room allocated to add 2 additional aisles to handle up to 8,000 orders per day in the future.